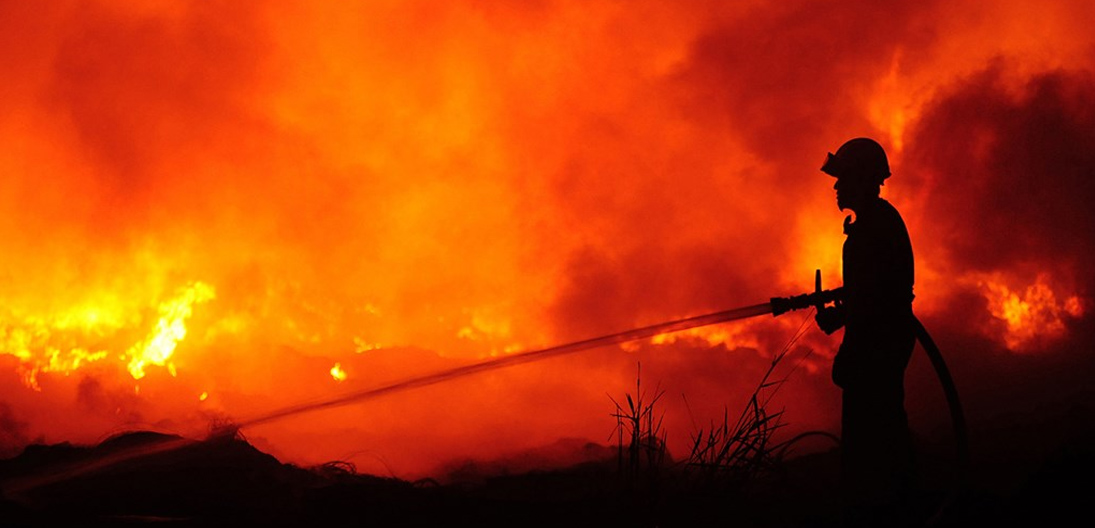
The consumption of polymer matrix composite materials is experiencing a continuous increase in a wide range of applications and sectors with flame-retardants. This is due to its good mechanical properties (high stiffness, strength and toughness), its low weight, its resistance to corrosion and its low cost. The long fibre composite materials are based on a homogeneous matrix and a fibre reinforcement that can be presented in different formats (fabric, threads, mats, etc.).
The fibres used as reinforcements are generally glass fibres (GF), carbon fibres or natural fibres, such as flax, jute, kenaf or hemp, among others. The fibre is impregnated by the matrix, which acts by transferring the loads to the fibres, as well as protecting the fibres from mechanical abrasion and environmental attack.
Between 35 and 40% of polymeric composites are usually manufactured with thermoplastic matrices, while the rest is composed of thermostable matrices. Thermoplastic matrices are gaining increasing interest, but its greater difficulty in processing makes its use a limitation.
Thus, many industrial sectors use thermoset matrix composites to meet the requirements demanded in the electronic, aeronautical, automotive, rail, wind industry, etc., at competitive costs. To comply with all the variety of requirements demanded by the industry, a wide variety of thermostable resins have been developed and introduced in the market, which are mainly based on unsaturated polyesters, vinyl esters, phenol-formaldehyde oligomers, benzoxazines, cyanate esters, polyimides, epoxides and mixtures thereof. Thus, the versatility offered by all these types of resins and additives available in the market allows obtaining a large number of formulations. Additionally, the combination of resins with different types of reinforcements allows the design of multiple systems made to measure for various fields of application.
Remember that here at FireCrunch we focus on providing high quality and sustainable fire-resistant building boards for interior and exterior settings in both residential and commercial properties, a great example are our fire rated ceiling panels that help prevent fires in buildings.
The flammability processes
However, the use of composite materials is not suitable for all applications. Among the challenges they present for its application in high performance sectors, the improvement of fire behaviour properties stands out. Polymer composites, when exposed to elevated temperatures, can undergo chemical decomposition or pyrolysis, and the resulting products can react with atmospheric oxygen during combustion.
The flammability process consists of five fundamental stages, which are: heating, decomposition, ignition, combustion and propagation.
To reduce the combustion capacity of composites, flame retardant functionalities in their chemical composition can be incorporated. This retardation can be achieved in two different ways: ‘reactive’ or ‘additive’.
The reactive form involves the design of new polymers with flame retardancy or the modification of existing polymers through copolymerization with flame retardant units (either in the chain or in a side group). In this way, the incorporation of the fireproof units in the polymer chain forms covalent bonds that suppose the contribution of retardancy to the permanent flame to the polymers, at the same time that the physical and mechanical properties of the original composite are maintained. However, the reactive form supposes a more complex procedure to achieve the required fireproofing properties of the systems to be used.
On the other hand, the additive form implies the incorporation of fire retardant or flame retardant loads to our polymeric systems. This form is the simplest and most economical way to bring flame retardancy to composites and that is why it is the most widely used form. However, it is important to bear in mind that this method involves certain drawbacks such as the compatibility between the load and the matrix, and the possible loss of mechanical properties in the polymer.
Flame retardants
A Flame Retardant (FR) is an additive capable of modifying, reducing, delaying or even eliminating the combustion process of materials. In this way, the main function of a flame retardant is to increase the escape time and, therefore, the response time to fight the fire and increase safety.
The most widely used flame retardant additives are mineral compounds, halogenated compounds, phosphorus-based compounds, nitrogen-based compounds, silicon-based compounds and nanometric particles.
Currently, flame retardants are mainly used in systems containing different flame retardant components. In this way a synergistic effect is achieved which improves the properties of the materials against fire with respect to the components separately. Thus, for example, the formation of a carbonaceous layer produced by a phosphorus-based flame retardant can be combined with the action in the gas phase produced by a halogenated flame retardant or, the same type of mechanism can be reinforced by combining two classes of FRs, such as nanoclays with phosphorus-based flame retardants, both acting in the condensed phase.
Another type of combination of components to achieve flame retardancy in polymeric materials are the so-called intumescent systems. They are based on the formation of a voluminous and insulating layer that acts as protection through simultaneous carbonization and foaming. The formulation of an intumescent system consists of three components: (i) an acid source (phosphoric, sulfuric, boric acid, ammonium salts, amine or amide phosphates, organophosphorus compounds), (ii) a carbonizing agent (usually a carbohydrate), for example, starch, dextrins, sorbitol, mannitol, etc.) and (iii) a foaming or swelling agent (urea, melamine, polyamides, urea-formaldehyde resins, etc.). These systems can be used in a large number of polymers such as polyamides, polyesters, polyolefins, epoxy and styrenics. The new intumescent systems are also an example of the synergistic effect against fire by combining different FRs.
Types of retardants
Among all the retardants that are currently on the market, it has been shown that the best properties to fight fire are obtained with halogenated additives. These additives had constituted most of the flame retardant solutions until new environmental directives appeared, such as those of REACH, WEEE and RoHS, which currently restrict their use. This is due to the adverse effects produced both on the organism and on the environment, among which include toxicity, bioaccumulation, persistence in the body and long-range transfer through the trophic chain. That is why the new trends in additivities with flame retardants are based on the use of non-halogenated substances.
Among the non-halogenated flame retardants, aluminium trihydrate (ATH or Al (OH) 3) is the most widely used flame retardant, which together with other metal hydroxides such as magnesium and phosphorus-based additives are almost half by weight of the market (see figure 3). It is anticipated that phosphorus-based flame retardants will continue to record one of the fastest market gains, since they have been shown to be one of the best substitutes for halogenated FRs in terms of both cost and final performance. In addition, other FRs such as melamine will also continue to experience continued growth.
Remember that here at FireCrunch we focus on providing high quality and sustainable fire-resistant building boards for interior and exterior settings in both residential and commercial properties.