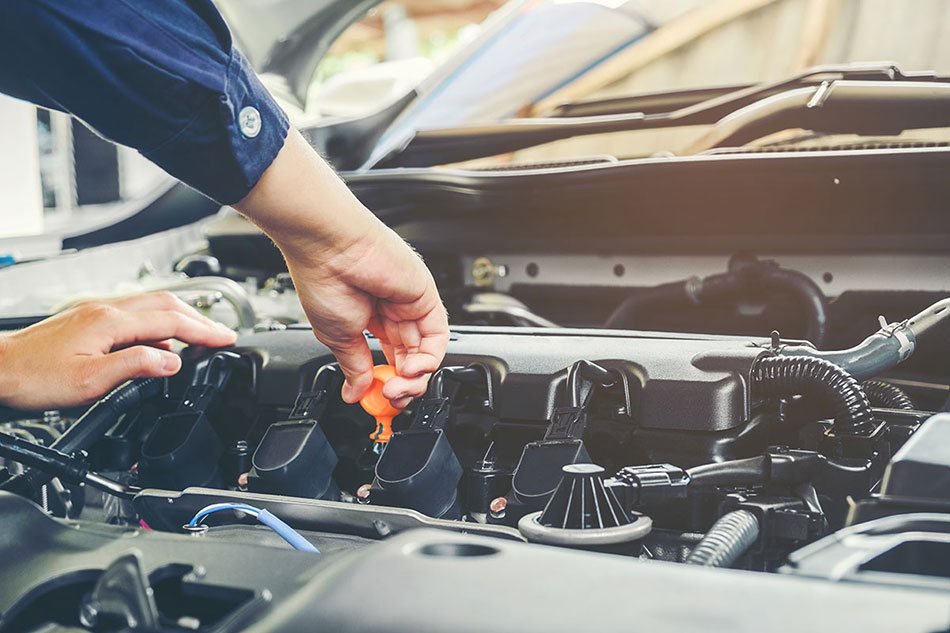
An injector is a component of the fuel injection system. Its mission is to spray, in a homogeneous manner and at the precise moment, a certain amount of fuel into the combustion chamber where, when mixed with the air at high temperatures, combustion is achieved. Thus, this article explains the operation of an injector and the parts that make it up, and the types of diesel injectors available in the market are exposed.
Here at Alpha Mobile Mechanics you are also part of the team, so we explain every detail related to the process and keep you aware of the way we complete this process. For more information about our services and how we can help you with on-spot diesel injectors maintenance do not hesitate to contact us. We’re expecting your call now!
Parts of an injector and operation
Diesel injectors are located on the cylinders (one injector for each cylinder), in the cylinder head and its movement is governed by the fuel pressure generated by the injection pump.
Each injector is controlled by the electronic control unit, which determines the amount of fuel that must enter the engine based on the need of the vehicle.
The injector is composed of the following parts:
- Nozzle holder: steel block that functions as a guide structure for the assembly of the rest of the components. Through this block, the fuel enters the pressure chamber of the injector.
- Nozzle (or injector): part fixed to the nozzle holder by means of a threaded sleeve. Inside the needle valve is mounted; This allows a tight pressure chamber to be formed since the tip of the same clogs the outlet holes of the injector.
- Needle valve: piston that acts as an injection gate. In idle state the valve closes the fuel passage.
- Spring: spring whose resting force allows the valve to close tightly against the inlet outlet hole. The increase in fuel pressure falls on the conical flap of the valve and lifts it, overcoming the force of the spring. At this time, the fuel is injected through the holes in the injector into the combustion chamber of the cylinder. Once the injection is finished, the spring pushes the needle valve back against the sealing seat.
- Push rod: rod that communicates the movement between the needle valve and the spring.
- Adjustment screw: screw that allows to adjust the fuel injection pressure.
- Closing fitting: during the injection process, a small dose of fuel is filtered between the needle valve and the nozzle holder. In this way it is possible to lubricate the rest of the elements of the injector. The closing fitting seals the injector assembly and allows the return of the residual fuel to the tank.
- Types of diesel injectors
There are two types of injection systems: direct injection systems and indirect injection systems.
Direct injection systems, used in diesel engines, inject the fuel into the combustion chamber, while indirect injection systems do so outside the combustion chamber.
The diesel injectors of a direct injection system are integrated directly on the cylinder, therefore, the fuel dosing the injector enters directly into the combustion chamber of the engine. This type of injection is a more efficient system than indirect injection because it offers fuel savings and improves engine performance.
There are two types of direct injection depending on the method in which it is executed:
The common-rail method (‘common duct’) is an electronic fuel injection system. The fuel in the tank is sucked into the high-pressure pump. This is pumped at high pressure to the common duct, which acts as an accumulator and is responsible for sending the fuel to the cylinders through the injectors, controlled by solenoid valves by the electronic control unit.
The pump-injector method is an injection system in which each cylinder has a pump and an injector, therefore, the high pressure is generated directly in each cylinder, thus avoiding pipes and achieving higher pressures.
Breakdowns and maintenance tips
The condition of the injectors is directly related to the performance and the life of the engine and the fuel consumption. Normally, a breakdown in the injectors is evidenced by a drastic reduction in power and by the significant increase in consumption.
If the fault is located in an injector, the rest of the injectors will not be affected. However, in common-rail systems, it is advisable to replace all injectors to ensure the protection and balance of the engine.
The failures that require replacing the injectors are the following:
Wear or occlusion of one or more injectors. The vehicle pulls and gives off a smell of pure fuel. If the obstruction is detected well in advance, you can opt for cleaning the injectors by using additives or in the workshop, by means of ultrasound or decarbonizer, cheaper alternatives to replacement.
System stuck permanently open. The vehicle expels black smoke and the spark plugs are impregnated with fuel. Although this type of breakdown is uncommon, repair of the injection system is a complex and expensive task, therefore, it is essential to attend to prevention by following these recommendations:
Perform preventive and predictive maintenance tasks respecting the deadlines recommended by the vehicle manufacturer, especially when replacing the fuel filter (commonly, every 30,000 km).
Do not rush the fuel tank below a quarter of the tank to prevent fuel sediments from entering the circuit.
Ensure the origin and quality of fuels. In the case of filling the tank with the wrong fuel, it must be emptied with the utmost urgency and purge the circuit.
Adding injector-cleaning additives is an option to prevent blockages. However, you always have to comply with the product specifications and the manufacturer’s recommendations.
Like any engine element, diesel injectors require basic maintenance. It is important to comply with the warnings described to avoid major breakdowns.
Here at Alpha Mobile Mechanics you are also part of the team, so we explain every detail related to the process and keep you aware of the way we complete this process.